In the realm of manufacturing, the term “investment casting foundry” might not immediately strike a chord with everyone. However, those in the know understand that these specialized facilities are the backbone of producing high-precision metal components.
Investment casting, also known as lost-wax casting, is a process that has stood the test of time, evolving from its ancient origins to become a modern marvel of engineering. Let’s delve into the fascinating world of investment casting foundries and explore their significance in today’s industrial landscape.
The ancient art of lost-wax casting
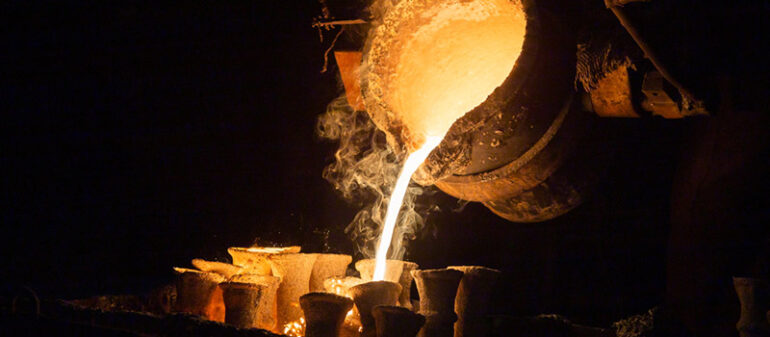
Investment casting dates back thousands of years, with its roots traced to early civilizations that used the technique to create intricate jewelry and religious artifacts. The process begins with creating a wax model of the desired part. This model is then encased in a ceramic shell, which hardens to form a mold.
Once the mold is set, the wax is melted away, leaving a cavity that is filled with molten metal. After cooling, the ceramic shell is broken away to reveal a meticulously cast metal component.
Modern applications of investment casting
While the basic principles of investment casting have remained unchanged, technological advancements have propelled the process into new realms of precision and application. Today, investment casting foundries produce components for a wide range of industries, including aerospace, automotive, medical, and military sectors.
The ability to create complex shapes with tight tolerances makes investment casting an invaluable technique for manufacturing parts that demand high accuracy and structural integrity.
The foundry environment
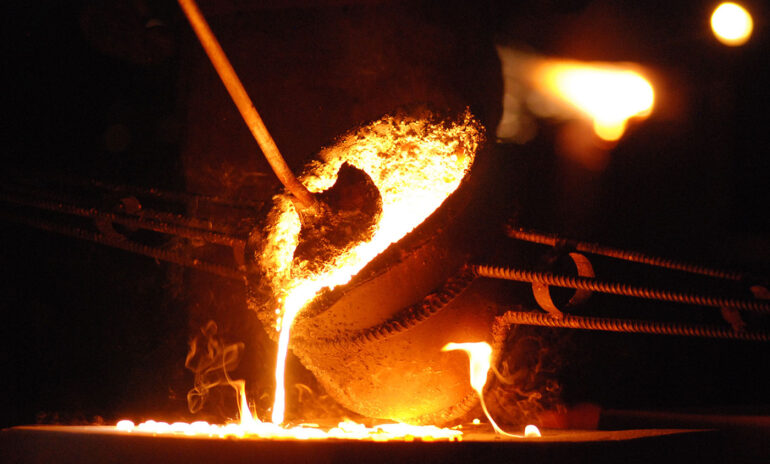
An investment casting foundry is a place where art meets science. The foundry environment is meticulously controlled to ensure the highest standards of quality and precision. Advanced equipment, such as computer-aided design (CAD) software and 3D printing, is often employed to create highly detailed wax patterns.
Additionally, modern foundries utilize cutting-edge materials and techniques to produce ceramic molds that can withstand extreme temperatures and pressures.
Benefits of investment casting
Investment casting offers several distinct advantages over other manufacturing processes. Firstly, it allows for the production of highly intricate and complex geometries that would be difficult or impossible to achieve through other methods.
Secondly, the process produces components with excellent surface finishes, reducing the need for additional machining and finishing operations. Furthermore, investment casting can work with a wide range of metals and alloys, providing flexibility in material selection based on specific application requirements.
Challenges and innovations
Despite its many advantages, investment casting is not without its challenges. The process can be time-consuming and requires a high level of expertise to achieve consistent results. However, ongoing innovations in materials science and process automation are helping to overcome these challenges.
For instance, the development of advanced ceramic materials and improved mold-making techniques are enhancing the durability and precision of ceramic shells. Additionally, automation and robotics are increasingly being integrated into foundry operations, reducing the potential for human error and increasing efficiency.
The future of investment casting foundries
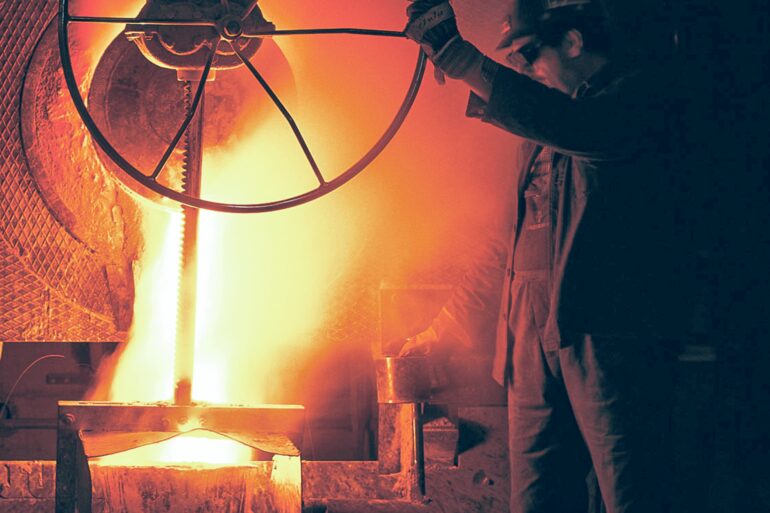
As industries continue to demand ever more precise and complex components, the role of investment casting foundries is set to grow. The integration of digital technologies, such as the Internet of Things (IoT) and artificial intelligence (AI), is poised to revolutionize the foundry environment.
These technologies will enable real-time monitoring and optimization of the casting process, further enhancing quality and reducing waste.
Moreover, the push towards sustainability is driving foundries to adopt more eco-friendly practices. Innovations in recycling and waste management are helping to minimize the environmental impact of investment casting, making it a more sustainable option for the future.
Conclusion
Investment casting foundries are at the forefront of precision manufacturing, combining age-old techniques with modern technology to produce components that are essential for various high-stakes industries.
As the demand for complex and precise metal parts continues to rise, these foundries will play an increasingly vital role in meeting the needs of the modern world. With ongoing advancements and a commitment to sustainability, the future of investment casting is bright, promising continued innovation and excellence in manufacturing.